I haven’t had a chance to sit down and write a proper post in a few weeks, and I thought I’d share a quick update on why that is / all that’s been going on behind the scenes here. I promise to share another knitting deep dive soon!
What’s been keeping me busy (& why I’m in London)
For the last six months I’ve been supporting The Sustainable Angle in preparation for their annual Future Fabrics Expo in London - and it’s coming up this week! Future Fabrics Expo is the largest dedicated showcase for sourcing certified, sustainably and responsibly produced materials for fashion, home & textile brands. A little highlight reel from London last year, if you’re curious:
I volunteered at the first NYC edition of the expo in November, and will be working with the team on this year’s NYC expo as well. If you work in sustainable fashion (especially if you’re in New York), mark your calendar for November 19th & 20th! And let me know if you’re interested to learn more about attending, partnering, speaking, etc.
Separately - while in London I couldn’t pass up the opportunity to check out Denier Studio, a yarn store dedicated to selling all ‘deadstock’ materials:
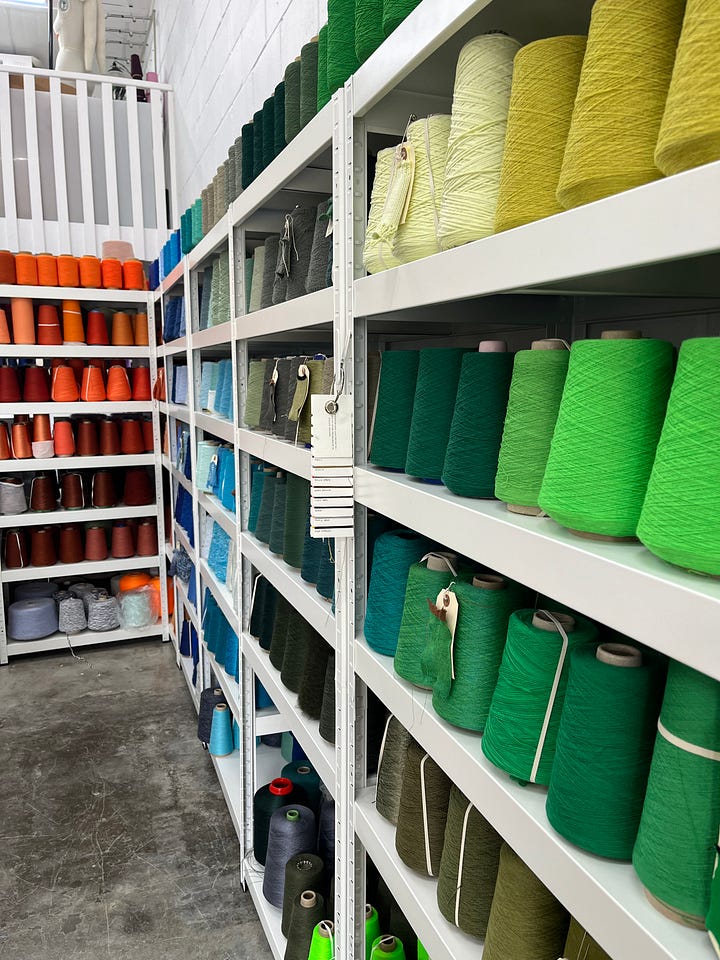
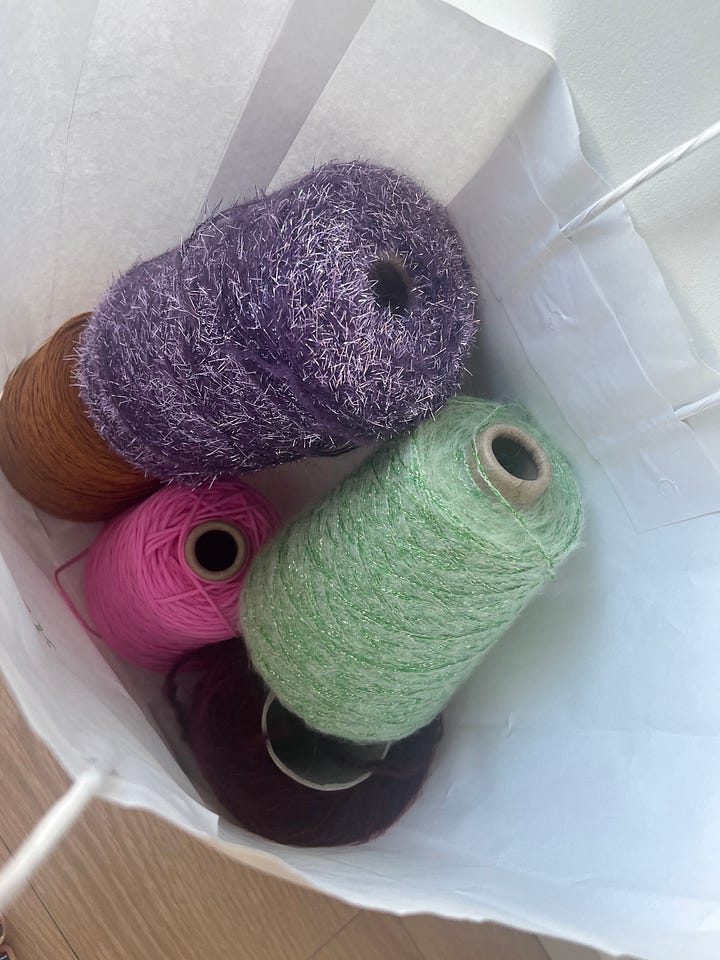
Threads of exploration
Aka some things that have been on my mind lately…
Because our current systems are optimized to make tons of new products, I’ve been thinking that the ‘unraveling’ part of my re-manufacturing lifecycle would present the most interesting opportunities for innovation. But a recent conversation with an experienced knitwear designer prompted me to re-frame my perspective: our current systems are optimized to make tons of ~the same~ new products. Meaning:
Every new design and new material needs to be tested and optimized, which makes ‘switching’ costs high. This is why manufacturers set minimum order quantities and offer volume discounts, effectively incentivizing overproduction (a lot more could be said on this topic - maybe in a future newsletter). I even experience this in my own small way - it’s tangibly faster and easier for me to knit a second sweater with the same materials than it is to knit a new design with new yarn.
Moving to more circular systems will require innovation at the design and manufacturing stages too - plugging unravelled yarn (as an example) back into existing production models isn’t enough. We’ll need to optimize for working with smaller quantities of a wider variety of materials, and get better at working with this new flavor of ‘feedstock’ - aka the materials we already have in circulation.
When I tell people I’m working in sustainable fashion, the question often comes up, “what does sustainable fashion really mean?”
There’s a lot of ways this question can be answered. But the one I keep coming back to is “the most sustainable clothes are the ones you already own*, regardless of brand and material”. The pieces that you ~actually~ wear, over, and over, and over again. *There’s so much more I could write about my own personal hypocrisies when it comes to fashion & sustainability, and my relationship to clothing and consumption. Another essay for another time…
I thought this recent piece about tailoring basics to make them fit perfectly was a fantastic example of this idea:
Enjoy!
Best,
Anne
Fantastic as always!